Heading out the door? Read this article on the new Outside+ app available now on iOS devices for members! Download the app.
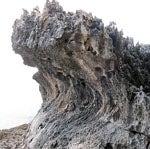
The rocky Caribbean island of Cayman Brac is a world-famous diving destination that was first developed for sport climbing in the mid 1990s. Within a few years, crags on the Brac began to experience the same rapid-corrosion issues as had Thailand. In February of 1998, a climber broke a low bolt on a two-year-old 5.11 route in the Orange Cave, hitting the very jagged ground and ending his climbing trip. Skip Harper, discoverer of climbing on the Brac, made the fortuitous decision to bring the broken bolt back to CSU in Colorado for analysis. The CSU metallurgists identified the failure mechanism as stress corrosion cracking—which none of the climbers had ever heard of. Harper replaced the bolt with a more expensive one made of marine-grade stainless steel.
John Byrnes is a retired engineer who owns a house on the Brac and would quickly become the island’s unofficial climbing ambassador. A string of accidents similar to the first one began to plague the Brac, and during that time Byrnes got a call from Mike Shelton, who wanted information about climbing on the island.
“I was embarrassed about the bolt situation,” recalls Byrnes, “and reluctant to talk about it, so I tried to tell Mike that the climbing was unsafe and not to go. He kept asking all these questions: What kind of steel was failing? What were the temperatures? What do the bolts look like? I just wanted to hang up, but he wouldn’t stop!”
Shelton, it turned out, was a welding metallurgist. He had just gotten back from Thailand and had been disturbed by the corroded bolts he saw there, and this problem sounded similar. “We ended up talking for over an hour,” says Byrnes. “We agreed to work together to make a bolt out of some new material. I still can’t believe we both made that commitment, right there on the phone.”
Byrnes sent a broken-bolt sample to Shelton. Unaware of the CSU’s finding, Sheldon independently concluded the problem was SCC. Shelton suggested three somewhat exotic alternatives: “duplex” stainless steel, Nickel-Hastelloy C (a nickel-based “super alloy”), and titanium.
Byrnes called climbing gear suppliers and general metal fabricators, but nobody was interested in producing the relatively small quantities he needed. Finally, Byrnes connected with Jim Bowes of the now-defunct company Ushba, which specialized in titanium climbing gear.
In spring of 2000, Bowes, Shelton, Harper, and Byrnes met at a Fort Collins pub and hashed out details for a new, corrosion-resistant bolt. “We drank, ate, and talked for hours,” says Byrnes. “By the end of the evening we had a design, material specs, cost estimates, a schedule—and a hangover.” And so, the “Tortuga” was born. Ushba delivered the first batch of these titanium glue-in bolts to Cayman Brac in November. That same year, Thailand also got a batch.
In the dozen years since, hundreds of titanium glue-ins have been installed in Thailand and Cayman Brac, with no bolt failures or any signs of corrosion. Titanium seems to work, but the solution did not come cheap. Including epoxy, the titanium glue-ins cost the anchor-replacement teams about $20 per bolt.
Ushba went defunct and the Tortugas are no longer made, but the new Eterna bolts from Titan Climbing look even better—and are even a little cheaper.